Complete quality management control process
1.QCC: Quality Assurance Circle. Including IQC, IPQC, FQC, OQC, QA, QE, TQC, etc.
2.IQC: Inspection of incoming quality. After the material demand order is issued, the company performs acceptance inspection on the products supplied by the supplier. IQC is established on this basis, and its role is to ensure the soundness of the company’s material inventory. Depending on the company’s material inspection standards, the number of people in this department will vary. Classes, groups, or classes can be set up (depending on the size standard) (full inspection, random inspection)
3.IPQC / PQC: Process inspection. After the acceptance of the materials, due to batch sampling and storage in the warehouse area, there will also be quality problems during the process. Therefore, when the product is online, it is required to determine the quality of the first product. Confirmation of parts and quality specifications and supervision during batch production. So as to improve the yield of process products and reduce costs
4.FQC: This is a comprehensive unit. Called warehouse inspection, also called final inspection (process). After the production is completed, the product flows to the offline line, that is, the package is put into storage. In the process, FQC will conduct a comprehensive quality inspection of the product, including packaging, performance, appearance and so on. Guarantee the performance, appearance, packaging of the stocked products and meet the requirements. According to the needs of customers and the need for production control, full inspection and packaging can be set. To put it plainly, it is a group of production personnel who are engaged in packaging inspection and storage after quality training, and are under the line process. It can also be completed by the production unit, and FQC will conduct random inspection and storage.
5.QA: Quality Assurance Engineer. This is a job description and should be said to be the quality assurance team. It is a unit within the company to improve the investigation of customer complaints, and propose process optimization programs to improve product quality.
6.QE: Quality Customer Complaint Processing Engineer. This is a unit for external quality description, processing, and coordination. It is a unit that directly coordinates, explains, and processes with the business and client. Including system file control, customer complaint 8D response, program file formulation, etc.
7.TQC: Total Quality Management. It is a new management concept, a new concept that brings quality into the fields of cost and delivery. On the basis of the original requirements for more fields, so as to improve corporate credibility and more comprehensive control of quality.
Six considerations for quality management
I. Quality Management Planning
1. Job responsibilities of the quality control department (including the duties of the quality control department, the duties of relevant personnel, and the duties of relevant work links).
2. Responsibilities of quality control of relevant departments (including overall duties of relevant personnel and specific duties of relevant departments).
3. Formulation and implementation of quality policy (including formulation of quality policy, implementation of quality policy).
4. Quality target formulation and implementation (including quality target formulation, quality target implementation).
5. Quality standardization management (including clarifying the role of standardization management, formulating standards, implementing standards, and revising standards).
6. Quality model management (including procurement model management, production model management, customer sample management).
Second, quality resource management
1. Implementation and management of quality training (including clarifying the purpose of training, determining the content of training, and implementing training).
2. Quality cost analysis (including quality cost classification, quality cost management division, and quality cost management steps).
3. Quality information management (including the quality information management process, the main content of the quality information center, the use of daily quality information)
Processing of quality information).
4. Quality management work environment management (including, determining the necessary factors of the work environment, establishing the necessary work environment, and maintaining the established work environment).
5. Relevant supplier management (including determining the needs of the supplier, establishing two-way communication with the supplier, determining the supplier’s process capability, and monitoring the supplier’s delivery status
Suppliers, encourage suppliers to implement continuous improvement programs, invite suppliers to participate in design and development activities, evaluate, confirm, and reward suppliers with excellent performance,
Internal Loss Cost Statistics Table 2 External Loss Cost Statistics Table 3 Identification Cost Statistics Table 4 Prevention Cost Statistics Table 5 Waste
Product Loss Summary Table Table 6 Information Liaison Table Table 7 Annual Supplier Evaluation Form).
Third, quality management tools
1. Section 1 Pareto chart method (including making Pareto chart, analyzing Pareto chart, precautions for using Pareto chart method).
2. Causality diagram method (including clarifying the principle of using causality diagram, making causality diagram, analyzing causality diagram).
3. Scatter diagram method (including making scatter diagram and analyzing scatter diagram).
4. Control chart method (including clear control chart principle and making control chart).
5. Association graph method (including distinguishing the types of association graphs and making association graphs).
6. Affinity diagram method (including determining the subject, forming a group, collecting information, writing cards, summarizing and organizing cards, making label cards, and drawing).
7. System map method (including determining the purpose, proposing means, measures, evaluation means, measures, making cards, preliminary drawing, confirming the purpose).
8. PDPC method (including clarifying the use of PDPC method and applying PDPC method).
9. Arrow-line diagram method (including clarifying the application range and application of arrow-line diagram).
Fourth, quality measurement management
1. Management of standard measuring instruments (including the implementation of classification and verification of standard measuring instruments, standardizing the use of standard measuring instruments, and clarifying standard measurement
Note on appliance management).
2. Management of general measuring instruments (including verification of general measuring instruments and use of general measuring instruments).
3. Energy measurement management (including clarifying the energy measurement scope, equipped with energy measurement equipment, verification and maintenance, and clarifying the precautions for energy measurement management)
4. Selection of measuring instruments (including the factors considered in selecting measuring instruments, options for uncertainty selection, and steps for selecting measuring instruments).
5. Calibration of measuring instruments (including calibration types and calibration precautions).
6. Guidance for the operation of measuring instruments (including electronic scales, spring scales, hardness testers, vernier calipers, height rulers 6, thickness gauges, micrometers).
7. Internal calibration standards for measuring instruments (including internal calibration standards for hardness testers, internal calibration standards for depth gauges, internal calibration standards for height gauges, internal calibration standards for outside micrometers, 200-500mm caliper internal calibration standard, 200mm caliper internal calibration standard, thickness gauge internal calibration standard, electronic scale internal calibration standard, steel tape internal calibration standard, temperature
Internal calibration standards).
8. Weekly inspection of measuring instruments (including making a weekly inspection schedule for measuring instruments, submitting a weekly inspection plan for the next year, submitting a weekly inspection plan for the next month, issuing a verification notice, conducting a weekly inspection, and using unqualified measuring instruments are strictly prohibited).
9. Hierarchical management of measuring instruments (including Class A management, Class B management, and Class C management).
Five, quality inspection control
1. Classification and selection of inspection (including classification according to inspection quantity, order according to production process, classification according to inspection site, and classification according to data nature
Classification, classification according to inspection method, classification according to inspection purpose, classification according to inspection cycle).
2. Formulation of inspection plan (including preparation of preparation of inspection plan, contents of inspection plan, and production of inspection flowchart).
3. Feed inspection (including feed inspection overview, feed inspection process, feed inspection items and methods, selection of feed inspection methods, processing of inspection results, emergency release control during feed inspection).
4. Process inspection (including the purpose of process inspection, first-piece inspection, roving inspection, online inspection, completion inspection, and final-piece inspection).
5, semi-finished product quality inspection (including semi-finished product process control, semi-finished product quality inspection).
6. Finished product inspection (including packaging inspection, finished product warehouse inspection and finished product shipment inspection).
Six, non-conforming product control
1. Analysis of the causes of non-conforming products (including product development and design, machine and equipment management, materials and accessories control, production operation control
System, quality inspection and control).
2. Non-conforming product standards (including selection of markers, application of markers).
3. Isolation of non-conforming products (including planning non-conforming product areas, placing signs, and controlling goods in non-conforming product areas).
4. Evaluation of non-conforming products (including application for disposal of non-conforming products, verification application, review and judgment, final review and judgment, arrangement for processing, re-verification,
The QC department classifies the allowable products in allowable income positions).
5. Disposal of non-conforming products (including conditional receipt, picking, rework and repair, return, scrap, and records of non-conforming products).
6. Prevention and control of non-conforming products (including {implementation of preventive measures for non-conforming products, and implementation of corrective measures for non-conforming products}
Seven, quality improvement plan
1. Quality improvement organization and operation (including overview of continuous quality improvement, continuous quality improvement organization and operation).
2. Quality improvement (including the establishment of environmental management leadership, establishment of quality improvement values, attitudes and behaviors, specific formulation of enterprise quality
(Improved goals, mutually reinforcing working relationships, continuing education and training for all employees)
3. Development of quality improvement activities (including identifying improvement opportunities, identifying improvement projects, establishing quality improvement organizations, formulating quality improvement plans, quality improvement
Problem diagnosis, formulation and implementation of quality improvement programs, control and evaluation of quality improvement, verification and confirmation of improvement effects, maintenance of improvement results,
Improve the determination of the project)
4. Implementation of CC activities (including quality control circle overview, QCC team formation, QCC activity development, QCC activity results summary, QCC results release,
QCC activity evaluation, CC common problem solving, QCC successful implementation skills)
5. Implementation of TQM activities (including TQM characteristics, TQM activity content, QC team construction)
6. Sigma management (including {6Sigma management basic connotation, 6Sigma management implementation key, 6Sigma management basic process implementation}
7. Implementation of non-defective plans (including clarifying the prerequisites for the implementation of non-defective plans, implementation of non-defective plans.
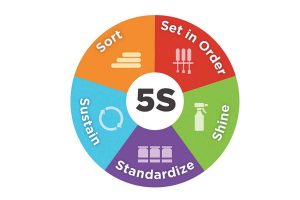
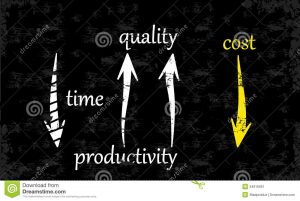