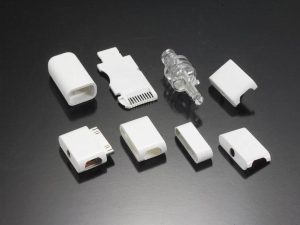
1.1 During the injection molding production process, the operator must make a self-inspection record to check the appearance of the product. The inspector should make the first signed seal of the product and fill in the “first inspection record card”. Product sampling inspections are required. Each inspection item must be complete. At the same time, the three links of packaged products, workbench products and machine random products must be verified at the same time. If problems are found, they should be corrected and coordinated in a timely manner. recording”;
1.2 The inspection requires the operator to rework the products that fail the self-inspection, and record, mark and review the reworked products until the product quality requirements are met, otherwise it is not allowed to stamp into the warehouse, and to ensure that the unqualified products are handed over during the shift The information is completely transmitted to the next inspection staff to prevent the accidental production and misuse of parts and materials;
1.3 The quality supervisor shall collect the inspection report every day and check the inspection records. If the records are inaccurate or in doubt, ask the relevant inspectors to understand and confirm. If it is careless, wrong, and inadequate, ask for notification and criticism. And the performance deduction will be assessed and deducted on the same day. Inspectors who have failed to implement the inspection work guidance for many times will consider changing posts or dismissing them;
1.4 After the finished products of each injection molding section are qualified, the inspection shall be stamped on the “Product Production Process Card” before entering the warehouse or transferring to the next process. The injection molded finished products, semi-finished products, qualified and unqualified products, etc. shall be in accordance with the specified area. Neatly placed and labeled in accordance with the principles of identification and traceability management, inspectors have the right to control and coordinate the process, and have the right to order employees to rectify or shut down for erratic identification.
2.1 Product inspection and confirmation after refueling
During the inspection process, when the machine is refueled or refilled, the inspection must confirm the quality parameters of the product’s appearance, engineering dimensions, performance strength and component assembly according to the first item inspection standard, and investigate and understand the materials used. Whether the batch has changed, which is convenient for recording and preventing the occurrence of badness;
2.2 Inspection and confirmation of products after mold repair
When the mold is abnormally repaired and the sample is finished, the inspection must confirm the quality parameters such as the appearance, engineering size, performance strength, and assembly degree of the product one by one according to the first item inspection standard, and check the previous samples to confirm that they are correct. Only after the mass production can be put into production, if the mold is a major maintenance issue, the quality engineer can pass the inspection according to the above items before mass production, and if necessary, a long-term verification and tracking is required;
2.3 Inspection and confirmation of products by newcomers
When the machine is replaced, newcomers work, etc., the foreman and inspection must strengthen the number of inspections, clearly inform the product attention and ensure that all employees understand, repeatedly check the proficiency of novice operations in the process, and correct any abnormalities in time. Change the operation of skilled employees at times to ensure the stability of quality;
2.4 Inspection and confirmation of products after water and power failure
During the production process, due to external reasons such as water outages and power outages, the machine was restarted for production. At this time, the machine’s work was in an unstable state. The inspectors should confirm the products one by one according to the first inspection standard. Appearance quality, engineering size, performance strength and component assembly degree, etc., and comparing with the previous samples, confirm that the product is qualified before mass production, and continue to follow up until the machine runs and the product quality stabilizes;
2.5 Inspection and confirmation of products after process adjustment
During the production process, the product mutates, and the workshop foreman or production supervisor readjusts the machine. After the original problem is overcome by changing the molding parameters of the machine, the inspection must reconfirm whether the quality of other inspection items has changed and whether various performances meet the requirements. For example, by increasing the temperature to overcome whether the poor appearance of the product will affect the physical properties of the plastic and make the product brittle, etc., to avoid new bad problems causing batch quality accidents;
2.6 Inspection and confirmation of products during shift
During the shifting process of the workshop, due to personnel changes, new material replacement has not been confirmed, the shift time has not been confirmed, the shift inspection has forgotten to complete the handover, or other reasons, etc., hidden quality risks for the production of the machine, which may cause the risk of batch quality accidents. In addition to the strict implementation of inspections, the successor inspectors must confirm the inspections and self-inspection forms of the shifts, understand the use of materials, etc., be familiar with the quality of the shifts in time, and take measures to ensure that changes in the ability to affect the process are timely done. Out reaction.
3.1 Concessions
When the production is urgently needed and the mold has problems, the process cannot be modified or the process control is negligent, and the batch problem caused the product to occur, the release review process should be strictly implemented. When the evaluation can be released, the workshop will apply for the release. After inspection and confirmation, engineering review Concessions will be released after approval by the relevant leaders. Relevant supervisors will implement their responsibilities and deduct penalties. Inspections of unprocessed products that have not gone through the approval procedures shall not be stamped, and warehouse management shall not be entered or reversed.
3.2 Rework Retest
When the process control is negligent or the employee fails to process the product according to the inspection requirements, resulting in defective batches that need to be processed, the workshop shall arrange employees to rework the product outside normal working hours in accordance with the “Regulations for the Management of Injection Molding Workshops”. The employees will be deducted and assessed. After rework, they will pass the inspection and re-inspection before passing the seal and entering the warehouse or reordering.
3.3 Disposal
The relevant provisions of the review and implementation process for the release of products. If they cannot be reused after review, they must be scrapped. The scrap should be scrapped by the production workshop, signed and confirmed by the relevant quality supervisor, and scrapped only after approval by the leader. Major general accidents must be referred to the general manager for decision. , Scrapped or abandoned privately, once found triple penalty.
4.1 The quality control personnel should promptly correct the problems found, analyze them, find out how to improve them, implement the control according to the corrective and preventive measures control procedures, contact the workshop for processing, and have the right to implement shutdown rectification for the unimproved machines and molds until the problem Can not be produced until it is resolved;
4.2 The handling of defective products must implement responsibilities, implement penalties, and implement corrective and preventive measures through investigation reports, order relevant departments and personnel to improve, and pass the quality department to verify that they are deemed to be closed. The follow-up process and feedback are handled by the quality department. Arrange implementation, other departments must cooperate to implement;
4.3 The improvement of the injection molding process involves modifying process documents or quality management documents in accordance with the requirements of document and data management procedures, and exploring the deficiencies and missing items in inspection specifications and operating instructions for the causes of abnormalities and out-of-control processes. To gradually improve process control documents and improve process control capabilities.
5. Quoting standards:
ISO9001: 2000 version of the relevant provisions of the “Quality Manual”, each program file.